Zastosowanie
Komory grzewcze są niezbędne w łańcuchach produkcyjnych, w których produkty, mieszaniny, surowce znajdujące się w beczkach lub pojemnikach być poddane obróbce cieplnej w celu przekazania ich do następnego etapu procesu produkcji.
Sektory referencyjne
Znajdują zastosowanie w takich w sektorach: chemicznym, kosmetycznym, farmaceutycznym, spożywczym, petrochemicznym, czy gazowym.
Dla kogo
Znacząco przyspieszają procesy podgrzewania surowców, co pozwala na skrócenie czasu produkcji. Ich wysoka efektywność energetyczna oraz dostosowanie do różnych potrzeb produkcyjnych sprawiają, że są idealnym rozwiązaniem dla firm dążących do optymalizacji kosztów i zwiększenia wydajności.
Budowa
Szafy grzewcze składają się ze spawanej ramy stalowej, do której przymocowane są ściany nośne wykonane z odpowiednio zmontowanych blach i paneli z izolacyjnej wełny mineralnej "wolnej od azbestu”.
Wytrzymałość konstrukcji
Szafy są zaprojektowane tak, aby wytrzymać naprężenia i niepożądane uderzenia przez długi czas podczas operacji załadunku i rozładunku. W tym celu na ścianach wewnętrznych wszystkich jednostek znajdują się konstrukcje ochronne, które zapobiegają uderzeniom przez palety. Konstrukcje nośne, z półkami na beczki, są poddawane obliczeniom konstrukcyjnym.
Izolacja termiczna
Konstrukcja jest odpowiednio zaizolowana, co zapewnia minimalne rozproszenie, efektywną wymianę ciepła i wynikającą z tego oszczędność energii.
Zobacz jak to działa
Proces wymiany ciepła
Proces wymiany ciepła odbywa się głównie poprzez konwekcję powietrza. Zespół wentylacyjny zainstalowany w górnej części komory zasysa powietrze, kierując je na element grzejny lub wymiennik ciepła zasilany cieczą, który kieruje ogrzane powietrze równomiernie na beczki lub pojemniki, tworząc turbulencje niezbędne do optymalnej wymiany ciepła.
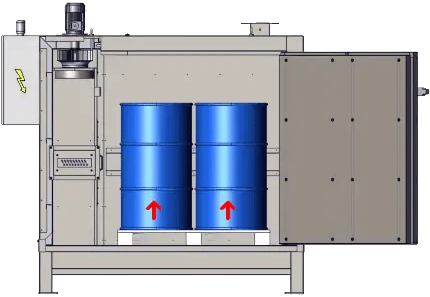
Kontrola temperatury
Proces jest "kontrolowany” przez cyfrowy regulator temperatury zainstalowany wewnątrz panelu sterowania i połączony z sondą zainstalowaną w odpowiednim miejscu.
STANDARDOWE KOMORY GRZEWCZE DO BECZEK
Najczęściej wybierane
MOŻLIWOŚCI I MODELE
Portfolio komór grzewczych TOPSERW składa się z 22 modeli o różnym przeznaczeniu różniące się od siebie:
Standardowe szafy grzewcze mogą być konfigurowane w zależności od:
Komora "z pojedynczą strefą grzewczą"
11 modeli z naszej oferty zaliczamy do standardowych komór grzewczych z "jedną strefą grzewczą” (patrz poniżej). Są one najbardziej poszukiwane na rynku, ich pojemność ładunkowa wynosi od 2 do 48 beczek 200 l, lub od 1 do 12 IBC 1000 l i posiadają pojedynczą strefę regulacji temperatury.
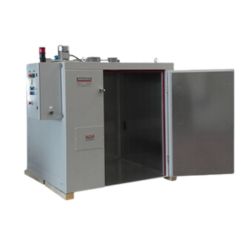
CC 001 S1
- pojemność: 2 beczki 200 l
- strefy regulacji: 1
- wymiary (S*G*W): 1580*1650*1950 mm
- liczba poziomów załadunku: 1
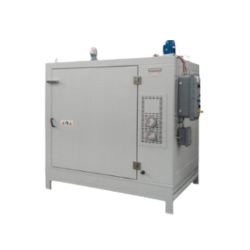
CC 002 S1
- pojemność: 4 beczki 200 l lub 1 IBC 1000 l
- strefy regulacji: 1
- wymiary (S*G*W): 2080*1650*1950 mm
- liczba poziomów załadunku: 1
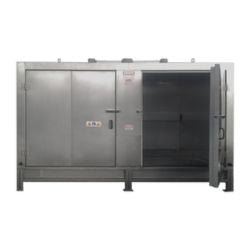
CC 003 S1
- pojemność: 8 beczek (poziomo) 200 l lub 2 IBC 1000 l
- strefy regulacji: 1
- wymiary (S*G*W): 3595*1650*1950 mm
- liczba poziomów załadunku: 1
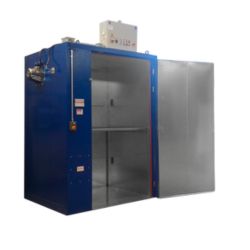
NC 004 S1
- pojemność: 8 beczek (pionowo) 200 l lub 2 IBC 1000 l
- strefy regulacji: 1
- wymiary (S*G*W): 2445*1650*2970 mm
- liczba poziomów załadunku: 2
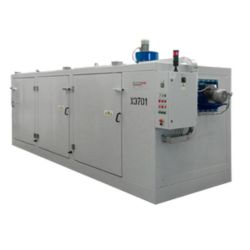
NC 008 S1
- pojemność: 12 beczek (poziomo) 200 l lub 3 IBC 1000 l
- strefy regulacji: 1
- wymiary (S*G*W): 5455*1650*1950 mm
- liczba poziomów załadunku: 1
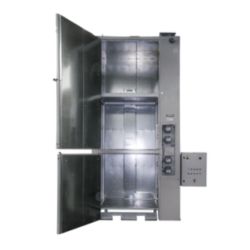
NC 029 S1
- pojemność: 12 beczek (pionowo) 200 l lub 3 IBC 1000 l
- strefy regulacji: 1
- wymiary (S*G*W): 2445*1650*4370 mm
- liczba poziomów załadunku: 3
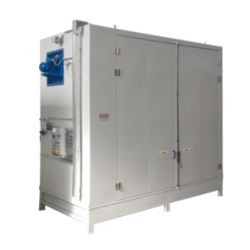
NC 007 S1
- pojemność: 16 beczek (pionowo) 200 l lub 4 IBC 1000 l
- strefy regulacji: 1
- wymiary (S*G*W): 3845*1650*2970 mm
- liczba poziomów załadunku: 2

NC 009 S1
- pojemność: 24 beczki 200 l lub 6 IBC 1000 l
- strefy regulacji: 1
- wymiary (S*G*W): 5455*1650*2970 mm
- liczba poziomów załadunku: 2
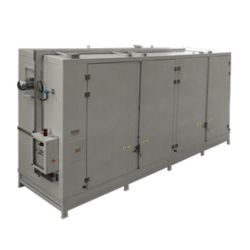
NC 013 S1
- pojemność: 32 beczki 200 l lub 8 IBC 1000 l
- strefy regulacji: 1
- wymiary (S*G*W): 6955*1650*2970 mm
- liczba poziomów załadunku: 2
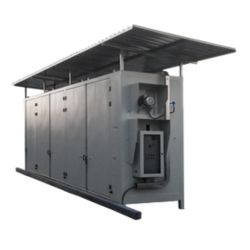
NC 015 S1
- pojemność: 40 beczek 200 l lub 10 IBC 1000 l
- strefy regulacji: 1
- wymiary (S*G*W): 8865*1650*2970 mm
- liczba poziomów załadunku: 2
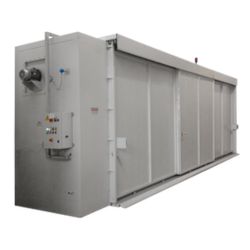
NC 028 S1
- pojemność: 48 beczek (pionowo) 200 l lub 12 IBC 1000 l
- strefy regulacji: 1
- wymiary (S*G*W): 9575*1650*2970 mm
- liczba poziomów załadunku: 2
Komory grzewcze "wielostrefowe”
Dla klientów, którzy przy bardzo zróżnicowanej produkcji muszą planować cykle grzania różnych produktów w różnych temperaturach, zaprojektowano 11 modeli "wielostrefowych” szaf grzewczych (patrz poniżej). Mają one możliwość załadunku od 4 do 48 beczek 200 l, od 1 do 12 IBC o pojemności 1000 l podzielonych na dwie lub więcej niezależnych stref.
Umożliwiają ogrzewanie różnych substancji w różnych temperaturach wewnątrz jednego urządzenia. Posiadają pojedynczy panel sterowania, co ułatwia użytkowanie. Zapewniają oszczędność energii dzięki możliwości ogrzewania wielu pojemników w tym samym czasie, a także dzięki możliwości włączania urządzenia strefowo.
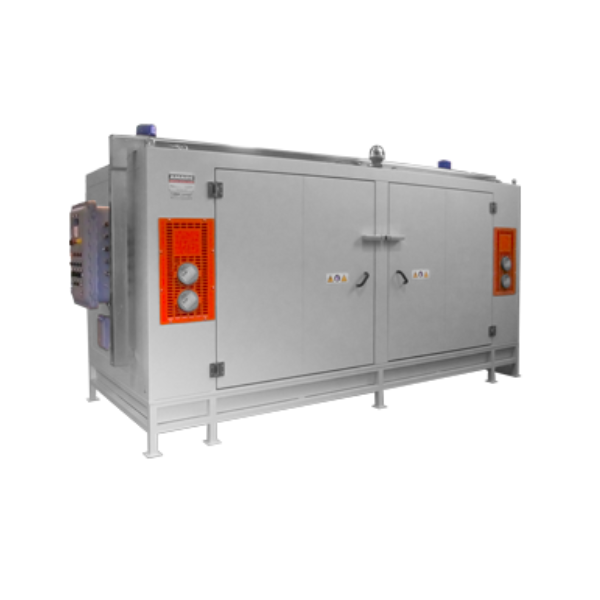
CC 006 S1 (8 beczek poziomo)
- pojemność: 4+4 beczki 200 l lub 1+1 IBC 1000 l
- strefy regulacji: 2
- wymiary (S*G*W): 4040*1650*1950 mm
- liczba poziomów załadunku: 1
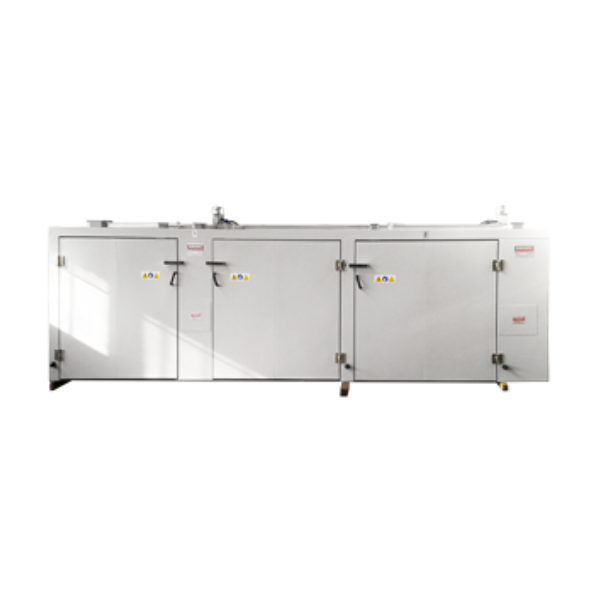
CC 010 S1 (12 beczek poziomo)
- pojemność: 4+8 beczki 200 l lub 1+2 IBC 1000 l
- strefy regulacji: 2
- wymiary (S*G*W): 5555*1650*1950 mm
- liczba poziomów załadunku: 1
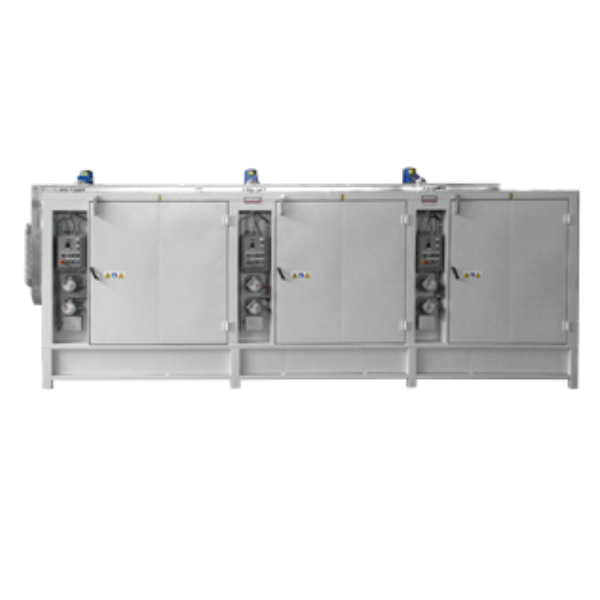
CC 029 S1 (12 beczek poziomo)
- pojemność: 4+4+4 beczki 200 l lub 1+1+1 IBC 1000 l
- strefy regulacji: 3
- wymiary (S*G*W): 6010*1650*1950 mm
- liczba poziomów załadunku: 1
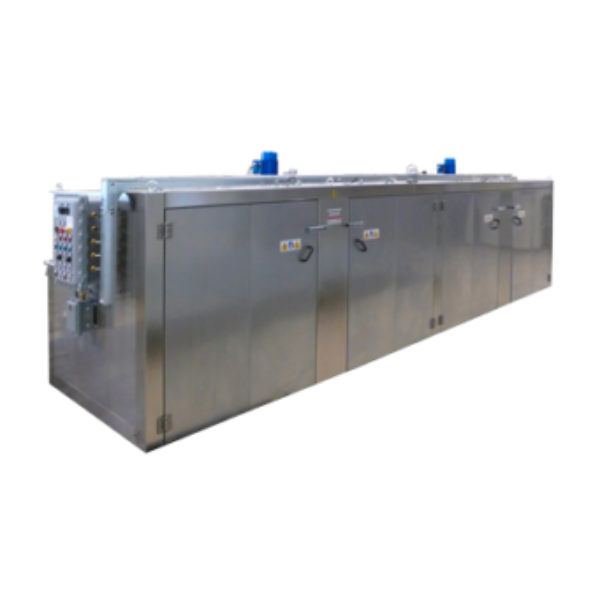
CC 012 S1 (16 beczek poziomo)
- pojemność: 8+8 beczki 200 l lub 2+2 IBC 1000 l
- strefy regulacji: 2
- wymiary (S*G*W): 7190*1650*1950 mm
- liczba poziomów załadunku: 1
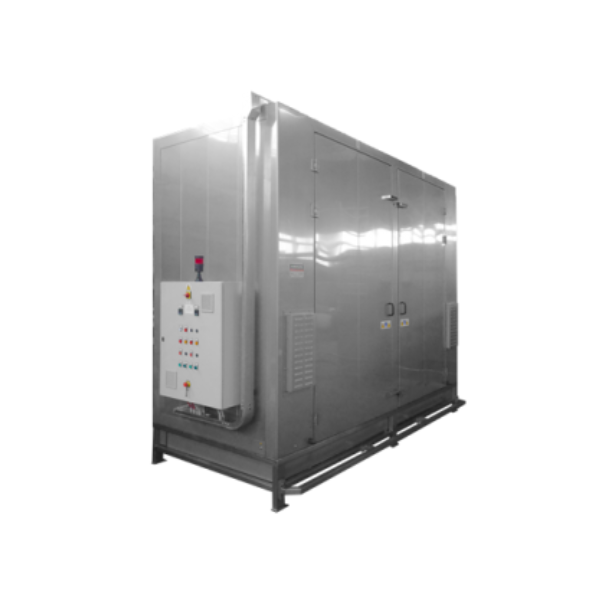
NC 005 S1 (12 beczek poziomo)
- pojemność: 8+8 beczki 200 l lub 2+2 IBC 1000 l
- strefy regulacji: 2
- wymiary (S*G*W): 4790*1650*2970 mm
- liczba poziomów załadunku: 2
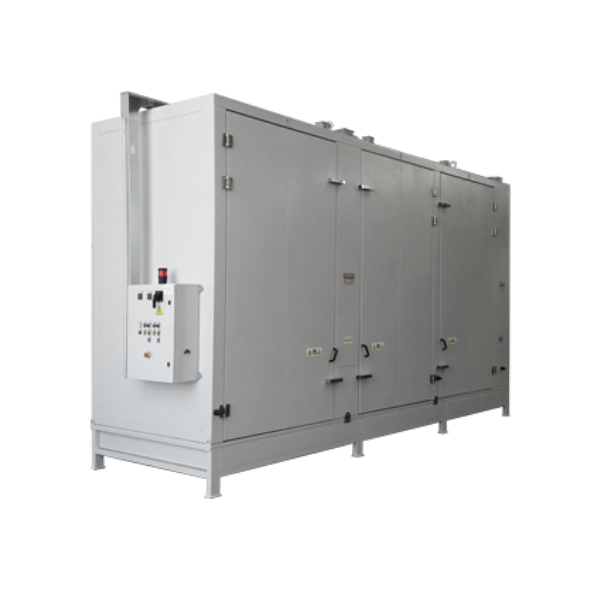
NC 016 S1 (24 beczki poziomo)
- pojemność: 8+16 beczek 200 l lub 2+4 IBC 1000 l
- strefy regulacji: 2
- wymiary (S*G*W): 6300*1650*2970 mm
- liczba poziomów załadunku: 2
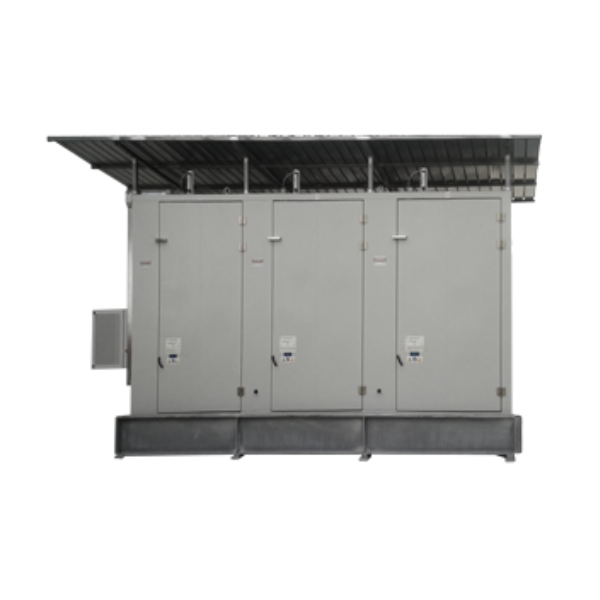
CC 018 S1 (24 beczki)
- pojemność: 8+8+8 beczki 200 l lub 2+2+2 IBC 1000 l
- strefy regulacji: 3
- wymiary (S*G*W): 6010*1650*2970 mm
- liczba poziomów załadunku: 2

NC 027 S1 (32 beczki)
- pojemność: 16+16 beczek 200 l lub 4+4 IBC 1000 l
- strefy regulacji: 4
- wymiary (S*G*W): 7950*1650*2970 mm
- liczba poziomów załadunku: 2
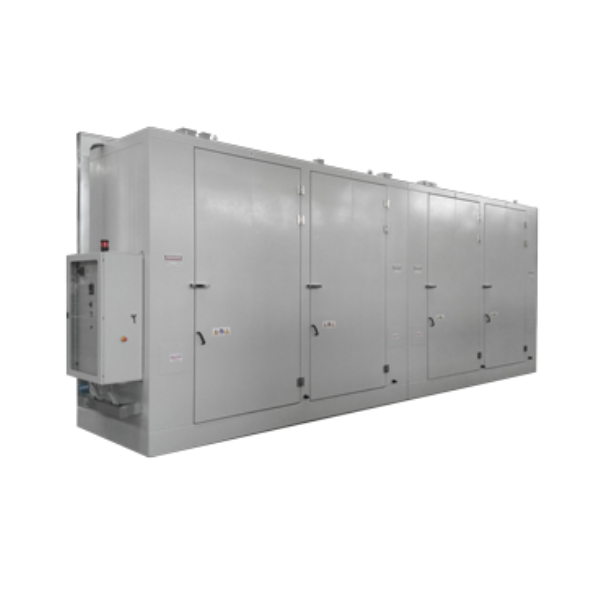
CC 030 S1 (32 beczki)
- pojemność: 8+8+8+8 beczki 200 l lub 2+2+2+2 IBC 1000 l
- strefy regulacji: 4
- wymiary (S*G*W): 7975*1650*1950 mm
- liczba poziomów załadunku: 1
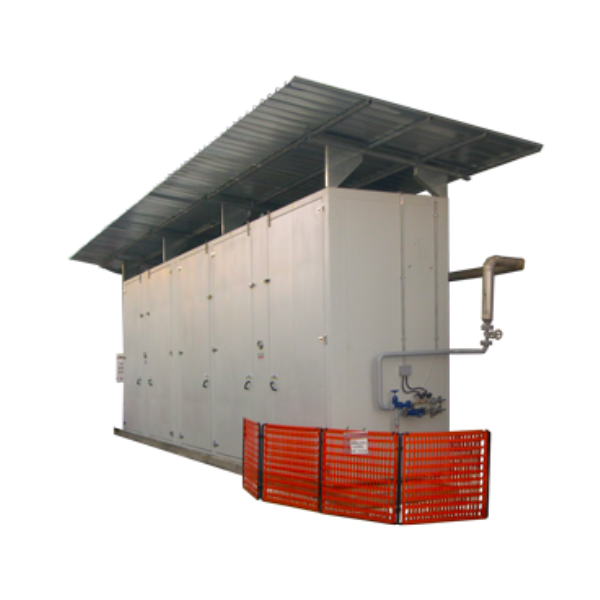
NC 018 S1 (40 beczek)
- pojemność: 16+24 beczki 200 l lub 4+6 IBC 1000 l
- strefy regulacji: 2
- wymiary (S*G*W): 9300*1650*2970 mm
- liczba poziomów załadunku: 2
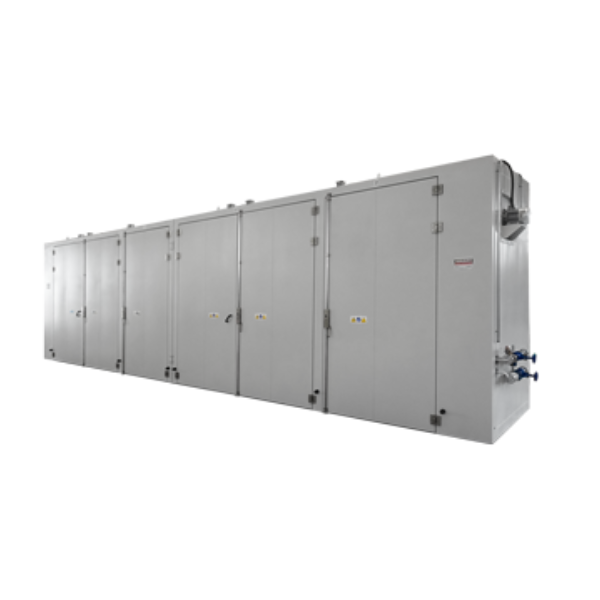
NC 017 S1 (48 beczek)
- pojemność: 24+24 beczki 200 l lub 6+6 IBC 1000 l
- strefy regulacji: 2
- wymiary (S*G*W): 10910*1650*2970 mm
- liczba poziomów załadunku: 2
PROJEKTY SPECJALNE
OPCJONALNIE
Normy Referencyjne UE
Wszystkie komory grzewcze objęte są zakresem stosowania Dyrektywy Maszynowej 2006/42/WE i odnoszą się do norm zharmonizowanych oraz norm europejskich dotyczących bezpiecznej konstrukcji maszyn.
Dyrektywa maszynowa 2006/42/WE; normy EN12100, EN60204-1, EN13849-1, EN62061, EN61508-1, 2, 6.
Wszystkie komory grzewcze zasilane parą, gorącą wodą, olejem Diathermic wchodzą w zakres stosowania dyrektywy 2014/68/UE – urządzenia ciśnieniowe "Artykuł 4, ustęp 3”.
Certyfikaty
Nasze rozwiązania cechuje niezawodność i gwarancja. Nasze bogate doświadczenie oraz ciągłe poszukiwanie coraz bardziej innowacyjnych rozwiązań i produktów pozwala nam pewnie oraz zdecydowanie zaznaczyć swoją obecność na dzisiejszym, stale rozwijającym się rynku.
W celu zapewnienia lepszych usług, w 2001 r. producent zaczął poddawać wszystkie swoje wewnętrzne procesom kontroli jakości. Firma uzyskała certyfikat ISO 9001:2015 w zakresie projektowania i budowy pancernych oporników elektrycznych, wymienników ciepła, pieców przemysłowych oraz paneli elektrycznych i paneli kontroli temperatury. Topserw także ma wdrożone systemy jakości i posiada Certyfikat Systemu Jakości PE-EN ISO 9001:2015.
Do Pobrania
POBIERZ PREZENTACJĘ KOMORY GRZEWCZE NA BECZKI I PIECE PRZEMYSŁOWE ORAZ KATALOG PRODUKTOWY
Pobierz prezentacjęPobierz katalog
USŁUGI
Serwis
Wizyta na miejscu
Za pośrednictwem techników lub naszych przedstawicieli handlowych odwiedzamy bezpośrednio miejsce instalacji, aby:
- sprawdzić miejsce, w którym ma być zainstalowany piec lub komora grzewcza
- przeanalizować specyfikacje projektu
- zrozumieć cele i oczekiwania klienta
- określić rozwiązania odpowiednie do zakresu projektu
Test ogrzewania
Przeprowadzamy testy nagrzewania produktów zgodnie ze zdefiniowanym protokołem, używając przyrządów do pomiaru temperatury skalibrowanych w certyfikowanych laboratoriach.
Testy ogrzewania można wykorzystać do oceny:
- krzywej nagrzewania materiału (nawet w przypadku zmiany fazy czas potrzebny do osiągnięcia przez materiał pożądanych warunków (takich jak temperatura i lepkość) w różnych warunkach pracy
- cech organoleptycznych materiału, które można również oceniać przez cały czas trwania badania (jeśli istnieją takie warunki).
FAT - Test odbioru fabrycznego
Na życzenie klienta przeprowadzamy testy odbiorcze przed wysyłką.
FAT jest wykonywany zgodnie z protokołem AMARC lub protokołem klienta, zgodnie z warunkami określonymi w umowie sprzedaży.
Opakowania
Wszystkie urządzenia są dostarczane w opakowaniach przystosowanych do transportu samochodowego.
Oferujemy także specjalne opakowania do transportu morskiego w postaci skrzyń drewnianych oraz worków barierowych.
Transport
Oferujemy i organizujemy usługi transportowe na terenie kraju i za granicą.
Korzystając z usług sprawdzonych, profesjonalnych i rzetelnych firm, uwalniamy naszych odbiorców od ciężaru poszukiwania i zarządzania usługami. W rzeczywistości wymiary i waga komór grzewczych mają decydujące znaczenie dla transportu i wiążą się z różnego rodzaju trudnościami organizacyjnymi.
Operacje rozładunku i pozycjonowania
Zapewniamy usługę "all inclusive” obejmującą transport, rozładunek i pozycjonowanie wykonywane za pomocą specjalnego pojazdu transportowego wyposażonego w dźwig i urządzenia przeładunkowe odpowiednie do tego celu.
Operacje rozładunku i ustawiania maszyny, które zwykle muszą być wykonywane przy użyciu dźwigu, wymagają wyspecjalizowanego personelu ze względu na krytyczny charakter operacji.
Rozpoczęcie użytkowania i szkolenie
Na życzenie zapewniamy usługę uruchomienia urządzenia w celu sprawdzenia prawidłowej instalacji i działania, po ustawieniu i podłączeniu do mediów. W ramach tej usługi nasi technicy przeprowadzą szkolenie dla operatorów, którzy będą odpowiedzialni za użytkowanie, instruując ich w zakresie najlepszych praktyk oraz wiedzy na temat zachowania zasad bezpieczeństwa.
Bezpłatna pomoc telefoniczna
Oferujemy bezpłatną pomoc telefoniczną świadczoną przez nasz wykwalifikowany personel. Tego typu wsparcie często jest w stanie natychmiast rozwiązać problem, jeśli dotyczy on kłopotów związanych z ustawieniami maszyny, co znacznie skraca czas przywrócenia sprawności operacyjnej.
Wsparcie "na wezwanie"
Nasi wyspecjalizowani technicy są gotowi do bezpośredniego i szybkiego działania "na miejscu” w zakładzie klienta w przypadku usterki lub zatrzymania maszyny, których nie można rozwiązać za pomocą wsparcia telefonicznego. Naszym celem jest maksymalne skrócenie czasu przestoju maszyny i ograniczenie problemów klientów.
Nadzwyczajna konserwacja i modernizacja
Pomagamy swoim klientom w operacjach nadzwyczajnych, takich jak:
- Dostosowanie maszyn do norm.
- Przełączanie źródła ciepła w urządzeniu z jednego systemu na inny, np. z elektrycznego na parowy.
- Modernizacja części mechanicznych lub całkowita wymiana drzwi, krat, itp.
- Przystosowanie maszyny do instalacji wewnątrz i na zewnątrz budynku.
Aplikacje
Proces suszenia polega na stopniowym usuwaniu pewnej części cieczy początkowo zawartej w produkcie poprzez jego ogrzewanie.
Istnieją różne metody suszenia (bezpośrednie, w strumieniu gazowym, w próżni), które różnią się w zależności od właściwości użytkowych wyrobu.
Piece suszarnicze AMARC umożliwiają ciągły pomiar i odczyt warunków dotyczących danych zmiennych (np. temperatury powietrza, produktu lub poziomu wilgotności).
Polimery to związki organiczne, których cząsteczki składają się z wielu identycznych, powtarzających się kolejno jednostek i powstają z prostszych substancji zwanych monomerami w wyniku reakcji polimeryzacji.
Z biegiem lat polimery zyskały ogromne znaczenie przemysłowe; w rzeczywistości mają one podstawowe znaczenie w przygotowywaniu tworzyw sztucznych, kauczuków, włókien syntetycznych oraz powłok ochronnych i klejących.
Istnieją różne reakcje polimeryzacji, a każda z nich wymaga określonych warunków przydatnych do jej przeprowadzenia, zależnych od wielu zmiennych.
Istnieją różne typy polimeryzacji, których klasyfikacja opiera się na mechanizmach reakcji lub etapach (polimeryzacja w masie, w roztworze, w zawiesinie, w emulsji).
W 1929 r. Wallace Hume Carothers wprowadził pierwsze rozróżnienie pomiędzy polimerami addycyjnymi a polimerami kondensacyjnymi, w zależności od tego, czy w wyniku reakcji polimeryzacji powstaje tylko polimer, czy również związek o małej masie cząsteczkowej (np. woda), zwany odpowiednio "kondensatem”.
Później, w 1953 r., Paul Flory dokonał rozróżnienia polimerów na podstawie mechanizmu reakcji. Proces łączenia polimerów odbywa się za pomocą dwóch możliwych mechanizmów chemicznych:
- polimeryzacja łańcucha
- polimeryzacja etapowa
Polimery otrzymane w wyniku polimeryzacji łańcuchowej są zazwyczaj polimerami addycyjnymi, natomiast polimery otrzymane w wyniku polimeryzacji stopniowej są zazwyczaj polimerami kondensacyjnymi. Istnieją jednak wyjątki: na przykład poliuretan jest polimerem addycyjnym, ale wytwarza się go za pomocą polimeryzacji stopniowej.
Klasy polimerów według klasyfikacji Carothersa i według klasyfikacji Flory’ego nie są więc identyczne.
Polimeryzacja przez addycję: proces ten jest stosowany do otrzymywania polimerów poprzez sekwencyjne, powtarzające się dodawanie jednego monomeru do drugiego. W tej reakcji nie dochodzi do eliminacji prostych cząsteczek, a jedynie do zmiany rozmieszczenia atomów.
Polimeryzacja przez addycję może obejmować dwa lub więcej różnych monomerów, dzięki czemu uzyskuje się kopolimery.
Polimeryzacja przez kondensację: dwa lub więcej monomerów reaguje tworząc nowe wiązanie, a proste cząsteczki (takie jak2 O, NH3, HCl) są eliminowane w reakcji; skład polimeru jest zatem inny niż skład produktów wyjściowych (inaczej niż w przypadku polimeryzacji przez addycję).
Polimeryzacja łańcuchowa: Reakcja jest wywoływana przez aktywowany gatunek (wolny rodnik, karbokation lub karbanion), zwany inicjatorem. Inicjator dodaje jedną cząsteczkę monomeru, tworząc nowe centrum aktywne, które z kolei dodaje kolejną cząsteczkę monomeru, tworząc kolejne centrum aktywne, i tak dalej, aż do końca łańcucha, który stopniowo rośnie.
Proces wytwarzania łańcucha polimerowego składa się z trzech etapów: inicjacji lub aktywacji, propagacji i zakończenia. Przykładem polimeru otrzymanego w wyniku polimeryzacji łańcuchowej jest polietylen.
Polimeryzacja etapowa: zachodzi między związkami chemicznymi posiadającymi dwa lub więcej reaktywnych końców (grup funkcyjnych), a więc zdolnymi do łączenia się ze sobą. Długie łańcuchy powstają w wyniku połączenia krótszych łańcuchów.
Przykładem polimeru otrzymywanego w procesie polimeryzacji stopniowej jest nylon.
Firma AMARC produkuje piece do polimeryzacji proszków, farb, żywic i powłok, a reakcja ta przebiega dzięki cyrkulacji gorącego powietrza wewnątrz pieca.
Piece AMARC można dostosować do potrzeb klienta pod względem wymiarów, temperatur roboczych, cykli termicznych, wymuszonego obiegu (masa gorącego powietrza jest kierowana do komory roboczej pieca i przenoszona przez regulowane deflektory w celu zapewnienia optymalnego przepływu) oraz możliwości polimeryzacji w cyklu ciągłym.
Degradacja różnego rodzaju materiałów obejmuje szereg procesów, które prowadzą do zmniejszenia ich właściwości i jakości.
Czasami, aby zachować niezmienione cechy wymagane od danego materiału/towaru (np. niektóre produkty w przemyśle spożywczym), należy utrzymywać te same warunki klimatyczne w sposób kontrolowany, tzn. w środowisku o odpowiedniej temperaturze, wilgotności i wentylacji, odpowiadającym danym zakresom.
Firma AMARC produkuje piece do składowania, które można dostosować do potrzeb klienta pod względem obrabianego materiału, wymiarów, zmiennych roboczych i wentylacji.
Piece AMARC są również wyposażone w system ustawiania i sterowania, który umożliwia konserwację i sprawdzanie, czy proces wewnątrz komory przebiega zgodnie z wcześniejszymi ustawieniami, co pozwala uzyskać określoną jakość produktu. Skomputeryzowany system umożliwia również podłączenie pieca do systemów fabrycznych, co pozwala na kontrolę i ustawianie procesu w czasie rzeczywistym oraz wyświetlanie sygnałów ostrzegawczych w przypadku wystąpienia błędów.
Obróbka stabilizująca umożliwia zapewnienie i utrzymanie pożądanego stałego, niezmiennego i trwałego stanu materiału bez znacznych wahań lub oscylacji parametrów.
Stabilizacja dotyczy kilku sektorów przemysłowych, takich jak sektor produkcyjny i spożywczy, a proces, który należy przeprowadzić, różni się w zależności od obiektów poddawanych obróbce i ich cech.
AMARC produkuje piece stabilizacyjne spełniające różne wymagania przemysłowe, których wspólnym mianownikiem jest wytwarzanie pożądanych warunków klimatycznych poprzez odpowiednią zmianę temperatury, wilgotności, wentylacji i oświetlenia w otaczającym środowisku.
W przypadku części metalowych firma AMARC produkuje piece przydatne do obróbki termicznej w celu odprężenia, odpuszczania i stabilizacji, czyli procesów mających na celu zmniejszenie lub wyeliminowanie naprężeń wewnętrznych i resztkowych w różnych typach produktów, zazwyczaj pochodzących z procesów obróbki na gorąco i na zimno, obróbki konstrukcji metalowych, obróbki hartowniczej i procesów mechanicznych, bez znaczącego pogorszenia właściwości mechanicznych materiału. W ten sposób można zapewnić stabilność wymiarową, obrabialność, dobrą jednorodność strukturalną części metalowych lub uzyskać kompromis pomiędzy odpornością i ciągliwością odpowiednią do warunków użytkowania materiału.
Piece AMARC są projektowane w zależności od metalu, który ma być poddany obróbce, oraz wymiarów elementów. Możliwe jest również przeprowadzanie obróbki w atmosferze obojętnej, aby uniknąć tworzenia się rdzy.
Proces suszenia przemysłowego polega na usuwaniu niezbędnej ilości cieczy zawartej w masie, np. wody zawartej w żywności, aby umożliwić jej dłuższe przechowywanie, a także na suszeniu proszków, farb lub różnych materiałów, takich jak glina i ceramika.
Aby ciecz zawarta w danej masie (śródmiąższowa, znajdująca się między warstwami lub włączona) odparowała, należy dostarczyć jej ciepła, dlatego produkt należy umieścić w suszarce.
Ilość cieczy zawarta wewnątrz części jest usuwana za pomocą różnych procesów, tj. dzięki odparowywaniu cieczy z powierzchni części oraz dyfuzji cieczy z wnętrza części na jej powierzchnię.
Główne czynniki, które należy wziąć pod uwagę w procesie suszenia, to:
- ilość płynu znajdującego się wewnątrz ciała i jego lepkość;
- wilgotność względna atmosfery i gradient wilgotności między powierzchnią części a jej wnętrzem;
- przepuszczalność, kształt, grubość i wymiary części.
Parowanie jest spowodowane przepływem gorącego powietrza o niskiej zawartości wilgoci w porównaniu z masą przeznaczoną do suszenia, które w sposób ciągły usuwa parujący płyn. Piece AMARC umożliwiają stałą kontrolę wilgotności i temperatury wewnątrz komory suszenia.
Różne procesy termiczne obejmują podgrzewanie wstępne, które umożliwia nadanie materiałowi odpowiedniej temperatury, a tym samym odpowiednich właściwości termofizycznych.
Podgrzewanie wstępne jest przydatne w procesie termoformowania (technika formowania na gorąco, w próżni lub pod ciśnieniem, tworzywa sztucznego z płyt lub folii), a nie w procesie mieszania.
Wstępne podgrzewanie polega na mniej lub bardziej długotrwałym wystawieniu materiału na działanie ciepła, tak aby osiągnął on wymaganą temperaturę. Proces wstępnego nagrzewania często umożliwia przeprowadzenie cyklu termicznego z kilkoma wzrostami temperatury i różnymi czasami stania: szybkość wzrostu temperatury, temperatura etapów pośrednich i końcowych oraz czas stania zależą od fizycznych i geometrycznych cech przedmiotu, który ma być poddany obróbce, oraz od potrzeby wstępnego nagrzewania.
W innych przypadkach konieczne jest podgrzanie produktu w celu przeprowadzenia go z fazy stałej do fazy ciekłej, aby nadać mu pewną lepkość niezbędną do kontynuowania procesu produkcyjnego.
AMARC produkuje piece i szafy grzewcze przydatne do wstępnego podgrzewania i topienia.
Piece AMARC do podgrzewania wstępnego można dostosować do potrzeb klienta pod względem obrabianego materiału, wymiarów, temperatur roboczych, cykli termicznych i wentylacji. Piece posiadają również możliwość programowania cyfrowego w celu kontrolowania temperatur, wilgotności i ogólnie warunków panujących w komorze pieca (możliwość programowania cykli termicznych na różnych etapach, z możliwością ustawienia prędkości zwiększania temperatury na każdym etapie [°C/min], różnych temperatur do osiągnięcia [°C], czasu utrzymywania poszczególnych etapów [min], automatycznego włączania wentylacji i rozpoczęcia ogrzewania, programowania temperatury wyłączenia). System sterowania pomaga kontrolować, czy proces przebiega wewnątrz komory zgodnie z wcześniejszymi ustawieniami, co pozwala uzyskać najlepszą jakość produktu. Piec może być podłączony do systemów fabrycznych, co umożliwia kontrolę i zarządzanie procesem w czasie rzeczywistym oraz ostrzeganie w przypadku wystąpienia błędów.
AMARC produkuje szafy grzewcze do materiałów znajdujących się w beczkach lub pojemnikach, takich jak smoła, żywice, smary, oleje i inne substancje, które przed użyciem muszą być utrzymywane w stałej temperaturze lub podgrzewane w celu zmiany ich lepkości.
Szafy grzewcze AMARC zapewniają równomierny rozkład temperatury, regulowany rozkład prędkości podgrzewania płynu. Pojemność komór modeli standardowych do 48 beczek o pojemności 200 l lub 12 pojemników o pojemności 1000 l (pojemność można zwiększyć w przypadku wersji niestandardowych). Solidna konstrukcja wykonana ze stali i paneli izolacyjnych sprawia, że urządzenie nadaje się do instalacji zarówno wewnątrz, jak i na zewnątrz budynków.
Wulkanizacja jest nieodwracalnym procesem, podczas którego, poprzez modyfikację chemiczną, polimer staje się mniej plastyczny, uzyskuje lub poprawia swoje właściwości elastyczne i staje się bardziej odporny na pęcznienie w kontakcie ze związkami organicznymi.
Wulkanizacja została odkryta w 1839 r. przez Charlesa Goodyeara. Goodyear odkrył proces wulkanizacji gumy przy użyciu siarki i zasadowego węglanu ołowiu. Stwierdził, że po podgrzaniu mieszaniny kauczuku naturalnego, siarki i węglanu ołowiu kauczuk przekształca się z materiału termoplastycznego w elastomer. W ten sposób odkrył zdolność lateksu kauczukowego do łączenia się z siarką w wysokiej temperaturze i przekształcania się w produkt o właściwościach mechanicznych i fizycznych lepszych niż kauczuk w stanie surowym (tracił on również całkowicie swoją kleistość), a także do znacznej poprawy właściwości elastycznych.
Większość przedmiotów gumowych po wyprodukowaniu jest poddawana wulkanizacji w warunkach wysokiej temperatury i ciśnienia. W niektórych przypadkach przedmioty są wulkanizowane w formach prasowanych za pomocą pras hydraulicznych, a w innych są poddawane wewnętrznemu lub zewnętrznemu ciśnieniu pary podczas ogrzewania.
Wulkanizacja to proces, który zależy od temperatury i czasu: wraz ze wzrostem temperatury należy konsekwentnie zwiększać szybkość wulkanizacji. Stosowanie wyższej temperatury w celu skrócenia czasu wulkanizacji jest jednak pewnym ograniczeniem: produkty wulkanizowane mogą zostać uszkodzone w wyniku działania bardzo wysokiej temperatury, może wystąpić tzw. zjawisko odwrotne, polegające na chemicznym rozkładzie produktu wulkanizowanego, co powoduje jego zmiękczenie i utratę elastyczności.
W zależności od procedury wulkanizacji, kształtu i grubości produktu, temperatury wulkanizacji mogą wahać się od temperatury otoczenia do około 300°C, a czas wulkanizacji może wynosić od kilku sekund do kilku godzin.
Różne rodzaje obróbki termicznej obejmują wypalanie, które oddziałując na temperaturę materiału, umożliwia uzyskanie określonych struktur i cech zgodnie z wymaganiami.
Wypalanie wiąże się z długotrwałym wystawieniem danego materiału na działanie ciepła i może być postrzegane jako sekwencja procesu nagrzewania i konserwacji, po którym następuje mniej lub bardziej kontrolowany proces chłodzenia.
W zależności od obrabianego materiału procesy te przyjmują różne nazwy, zależnie od temperatury, w jakiej przeprowadzana jest obróbka, oraz od chłodzenia. Na przykład w przypadku struktur metalurgicznych mamy do czynienia z wyżarzaniem, normalizacją, hartowaniem, wyżarzaniem miękkim i odpuszczaniem. Wypalanie dotyczy jednak również sektora produktów spożywczych, polimerów, glin, żywic, włókien węglowych itp.
Firma AMARC wyprodukowała piece, które można dostosować do potrzeb klienta pod względem obrabianego materiału, wymiarów, temperatur roboczych, cykli termicznych, wymuszonego obiegu (masa gorącego powietrza jest kierowana do komory roboczej pieca i przenoszona przez regulowane deflektory, aby umożliwić optymalny przepływ).
Piece AMARC są również wyposażone w system ustawiania i sterowania, który umożliwia konserwację i kontrolę, aby upewnić się, że proces wewnątrz komory przebiega zgodnie z wcześniejszymi ustaleniami, co pozwala uzyskać lepszą jakość produktu i większą wydajność procesu wypalania. Można również zainstalować system komputerowy, który umożliwia podłączenie pieca do systemów fabrycznych, z kontrolą procesu w czasie rzeczywistym i sygnałami ostrzegawczymi w przypadku wystąpienia usterek.
NASZE REALIZACJE
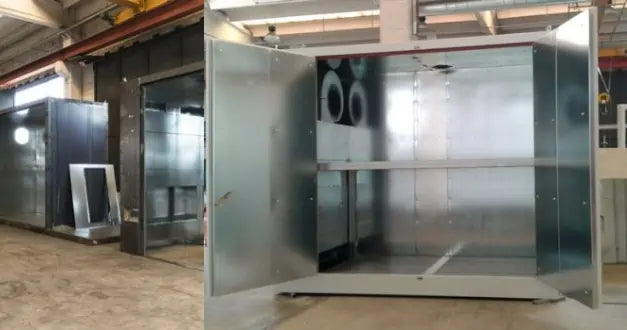
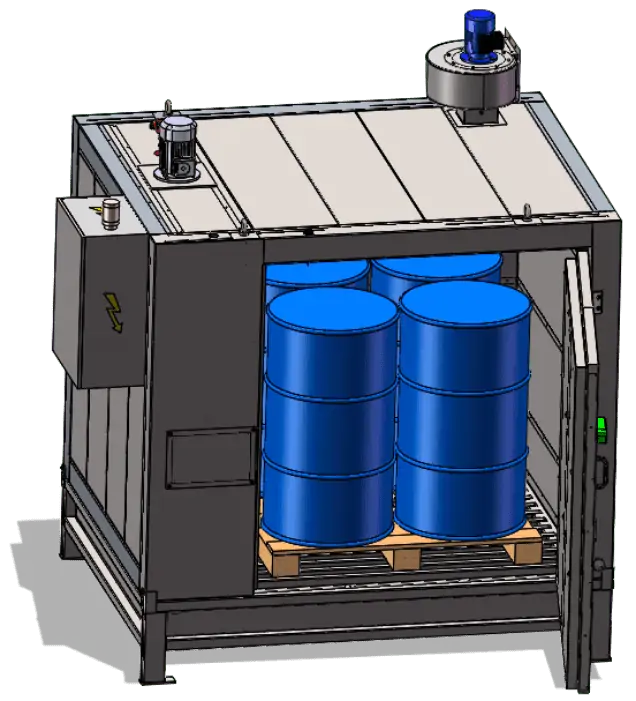
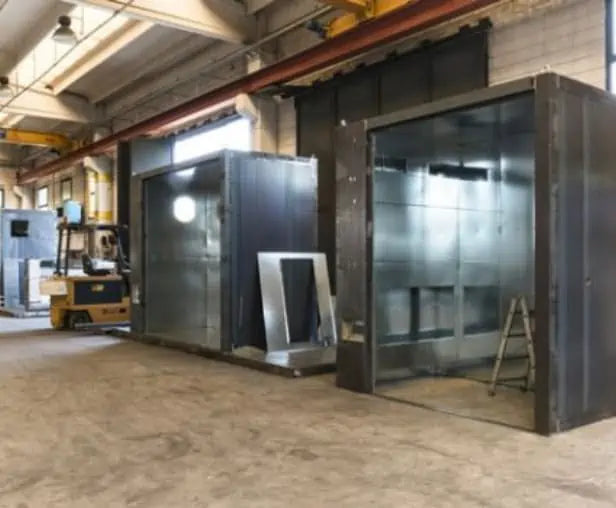
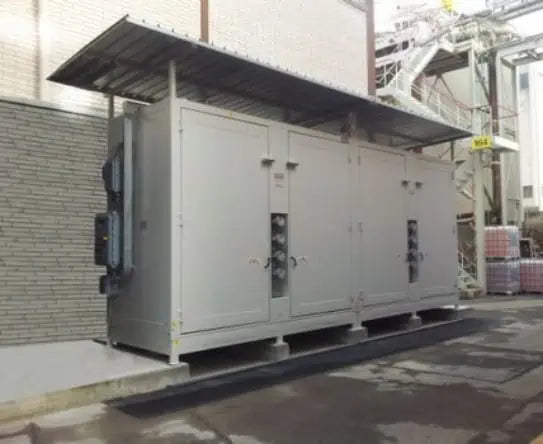
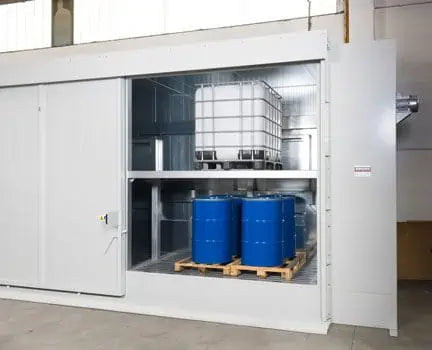

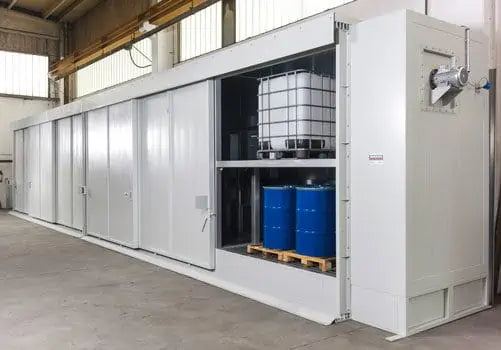

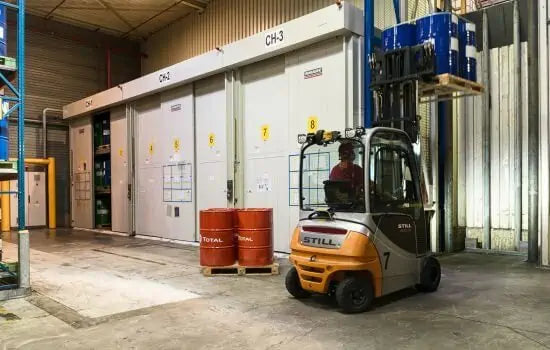
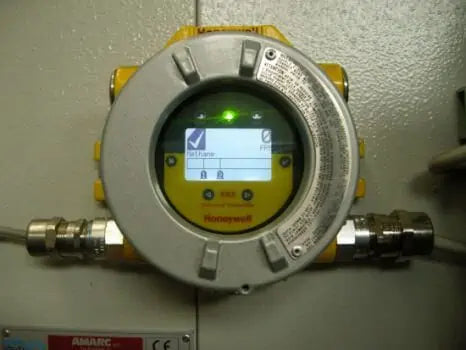
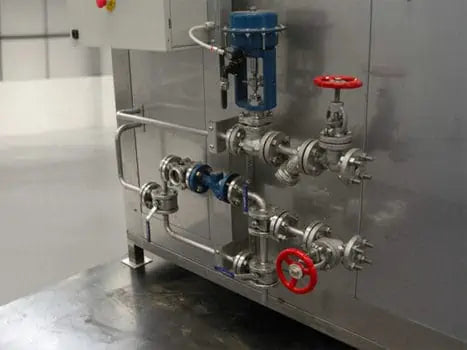
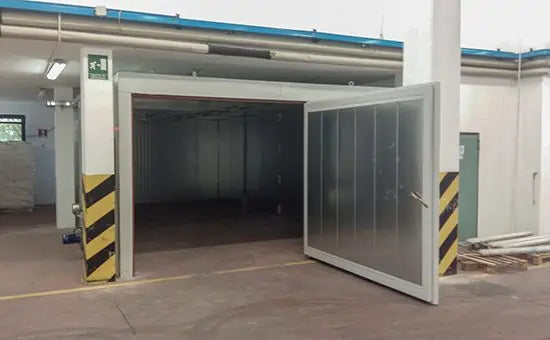
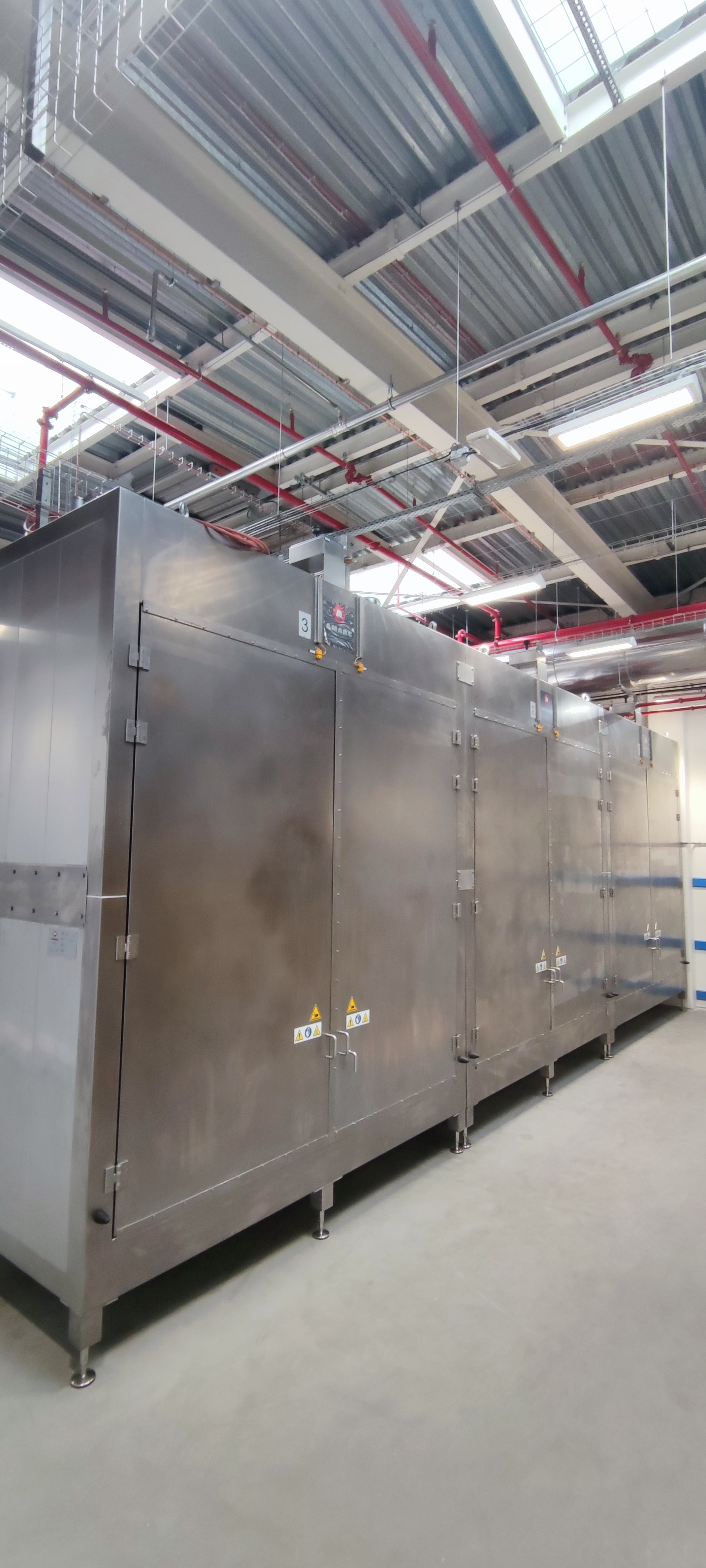
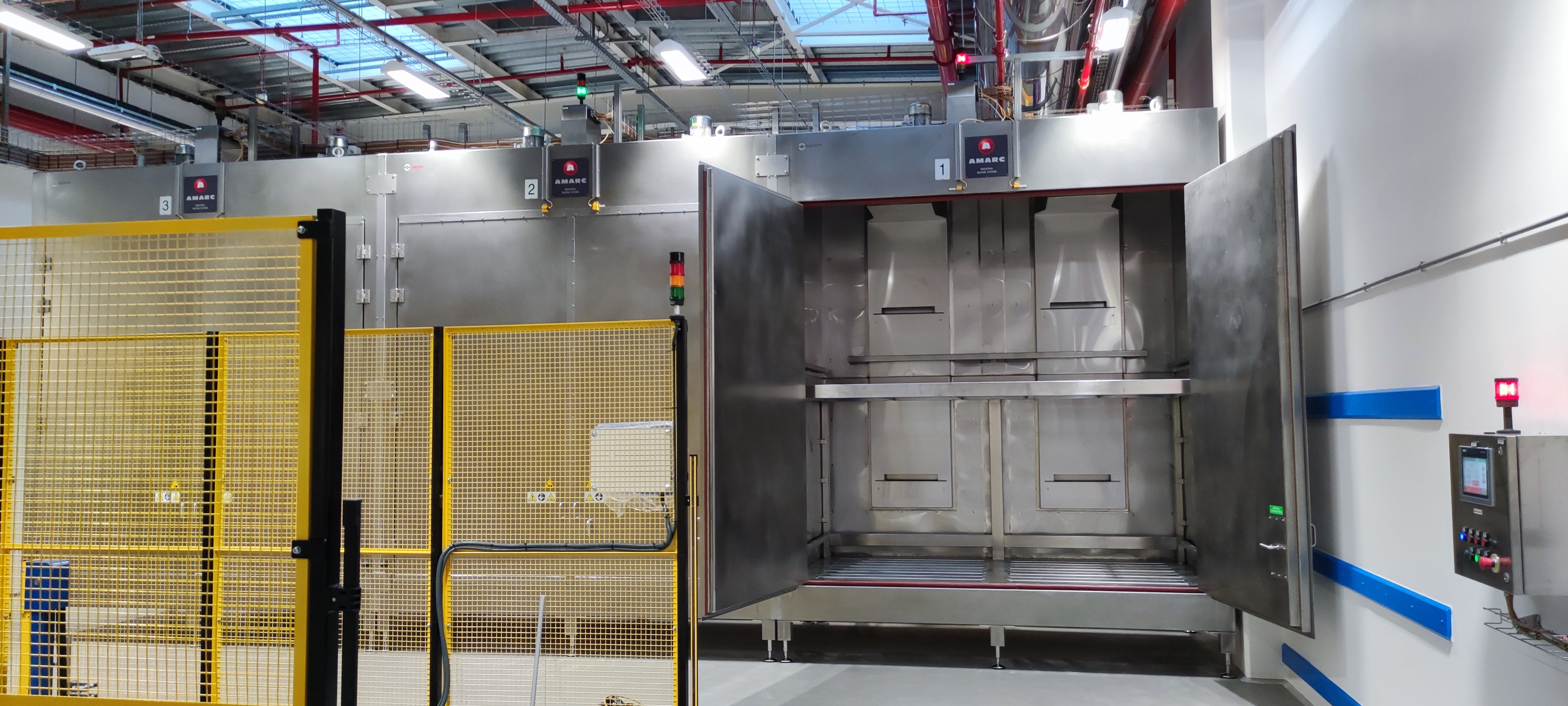
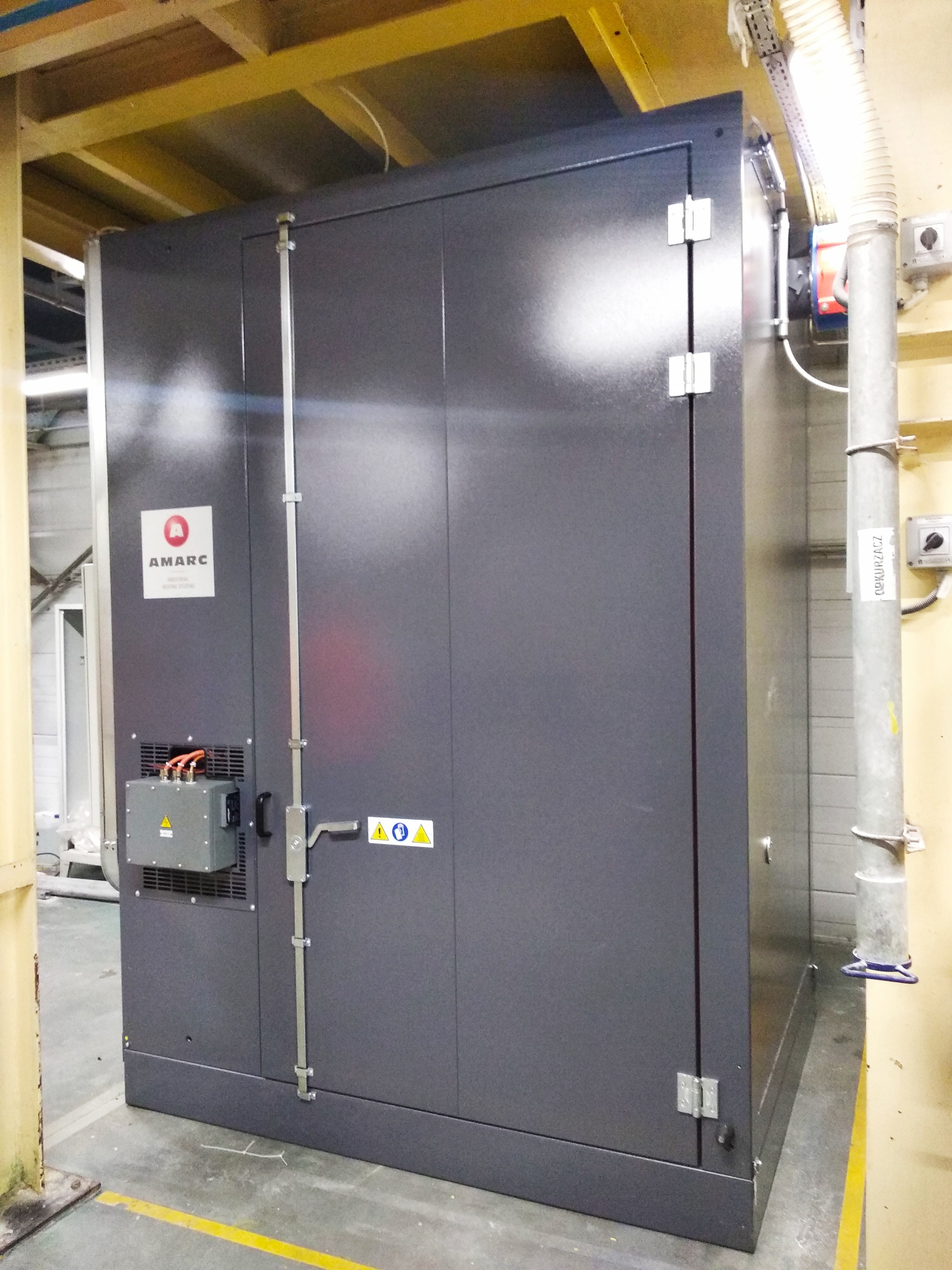
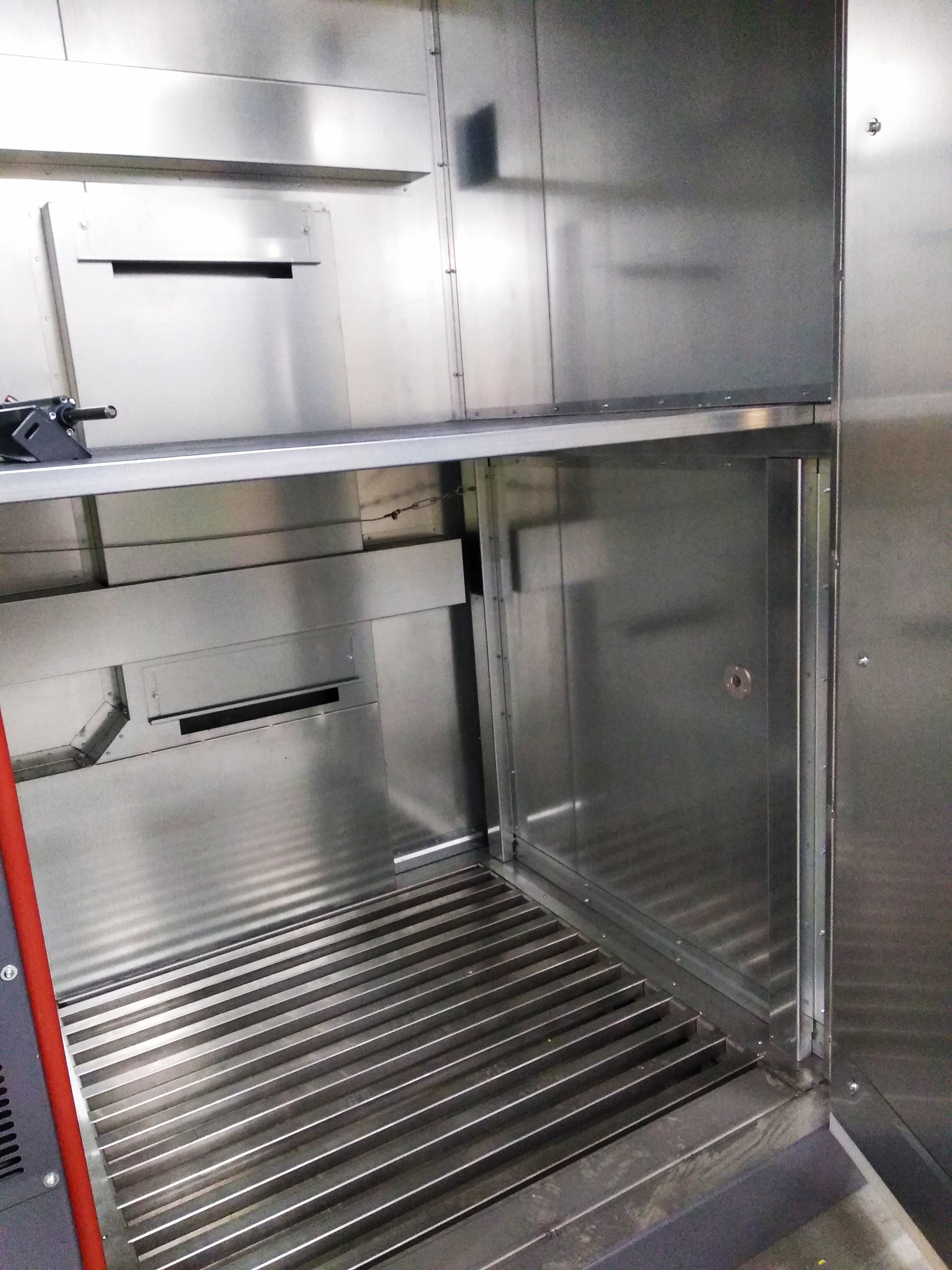
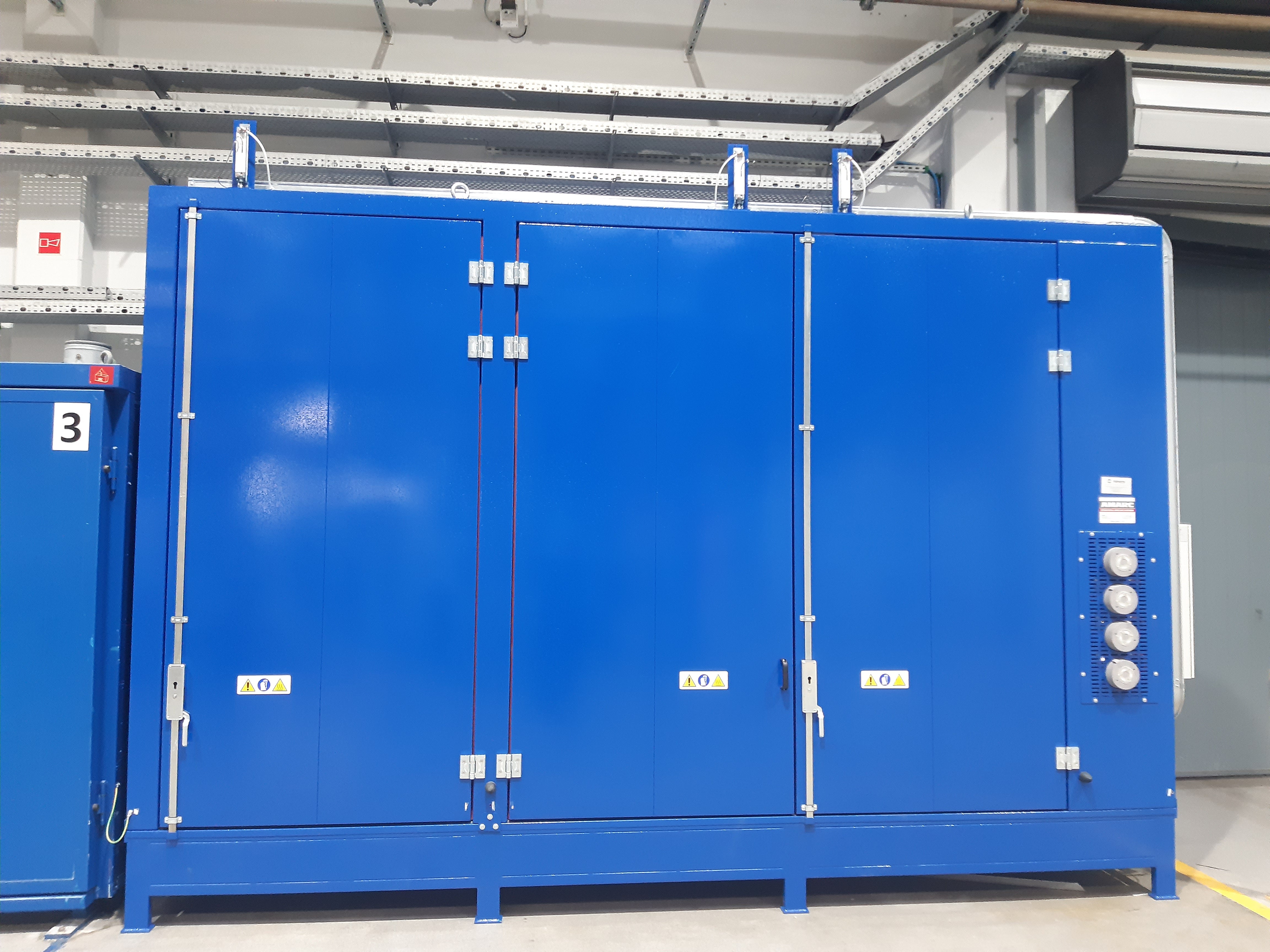
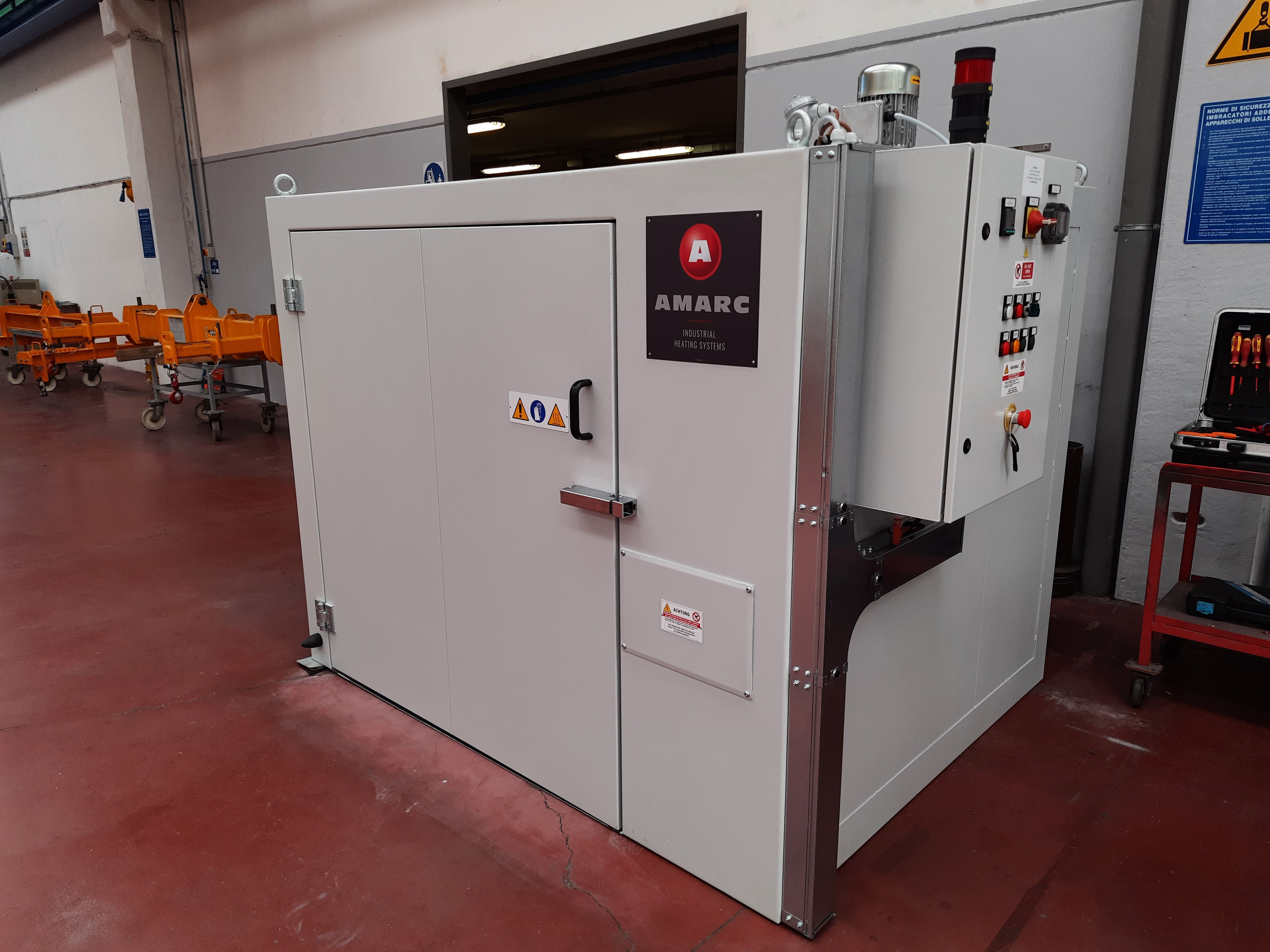
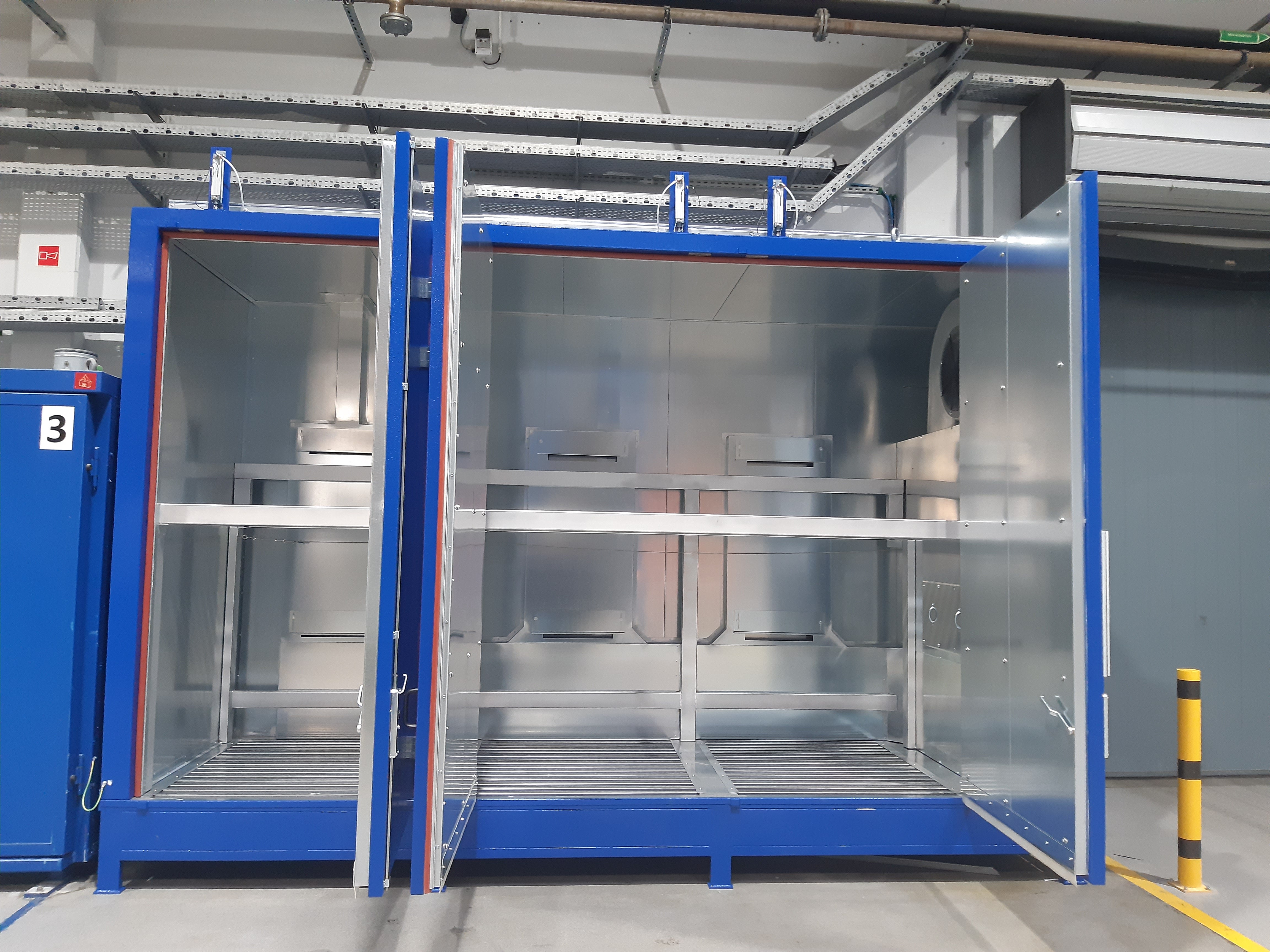
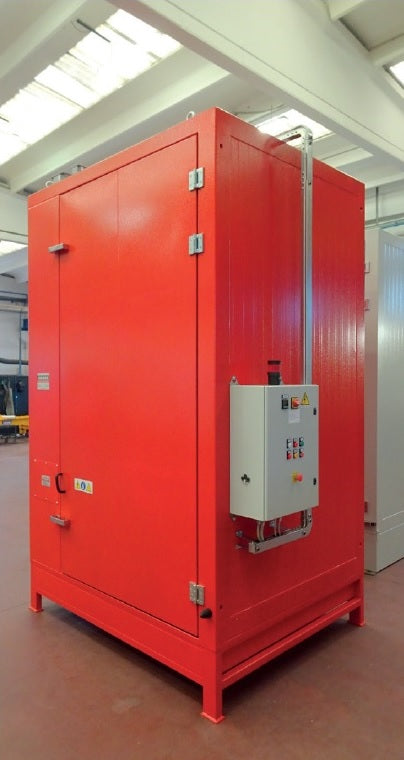
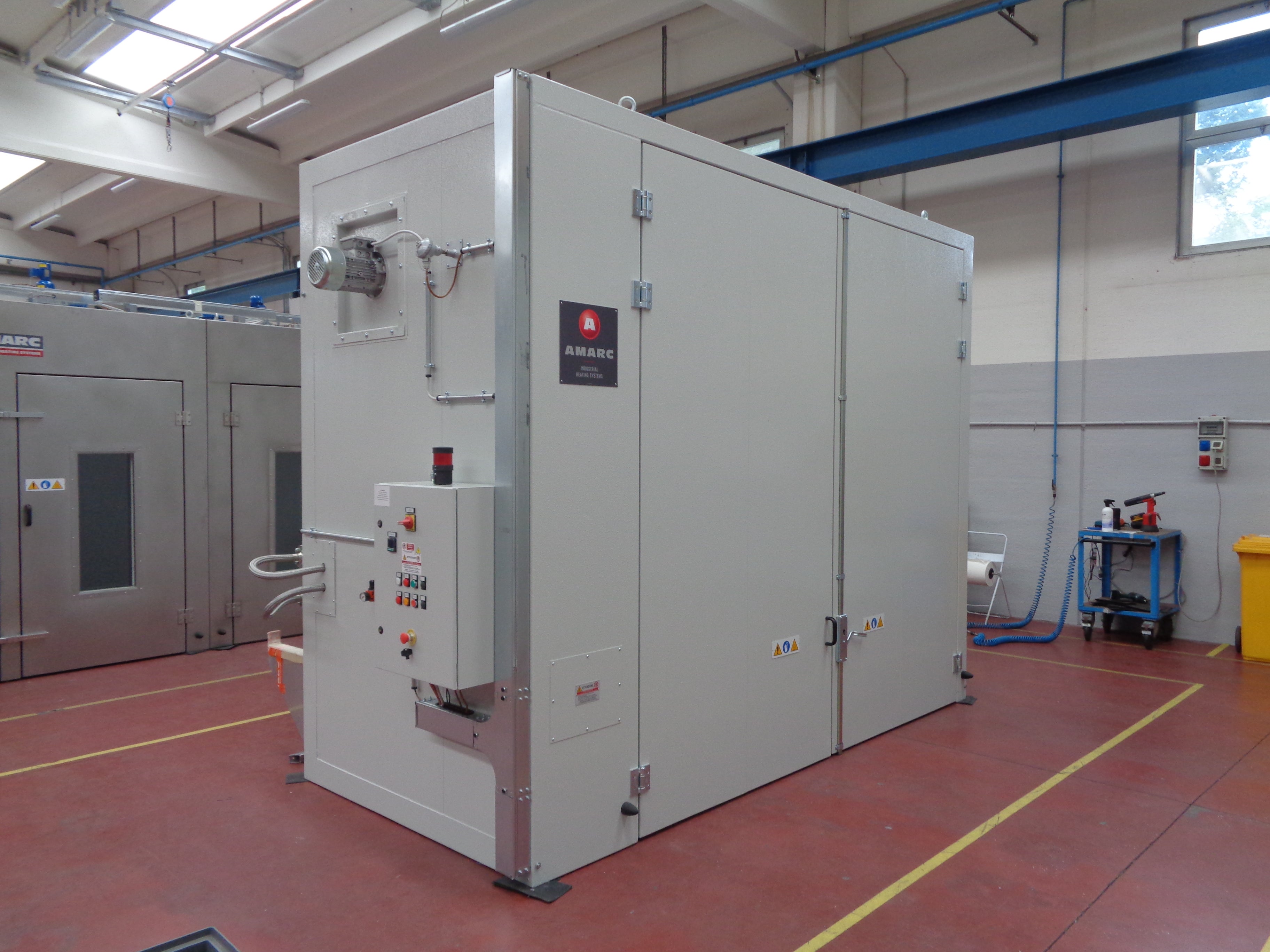
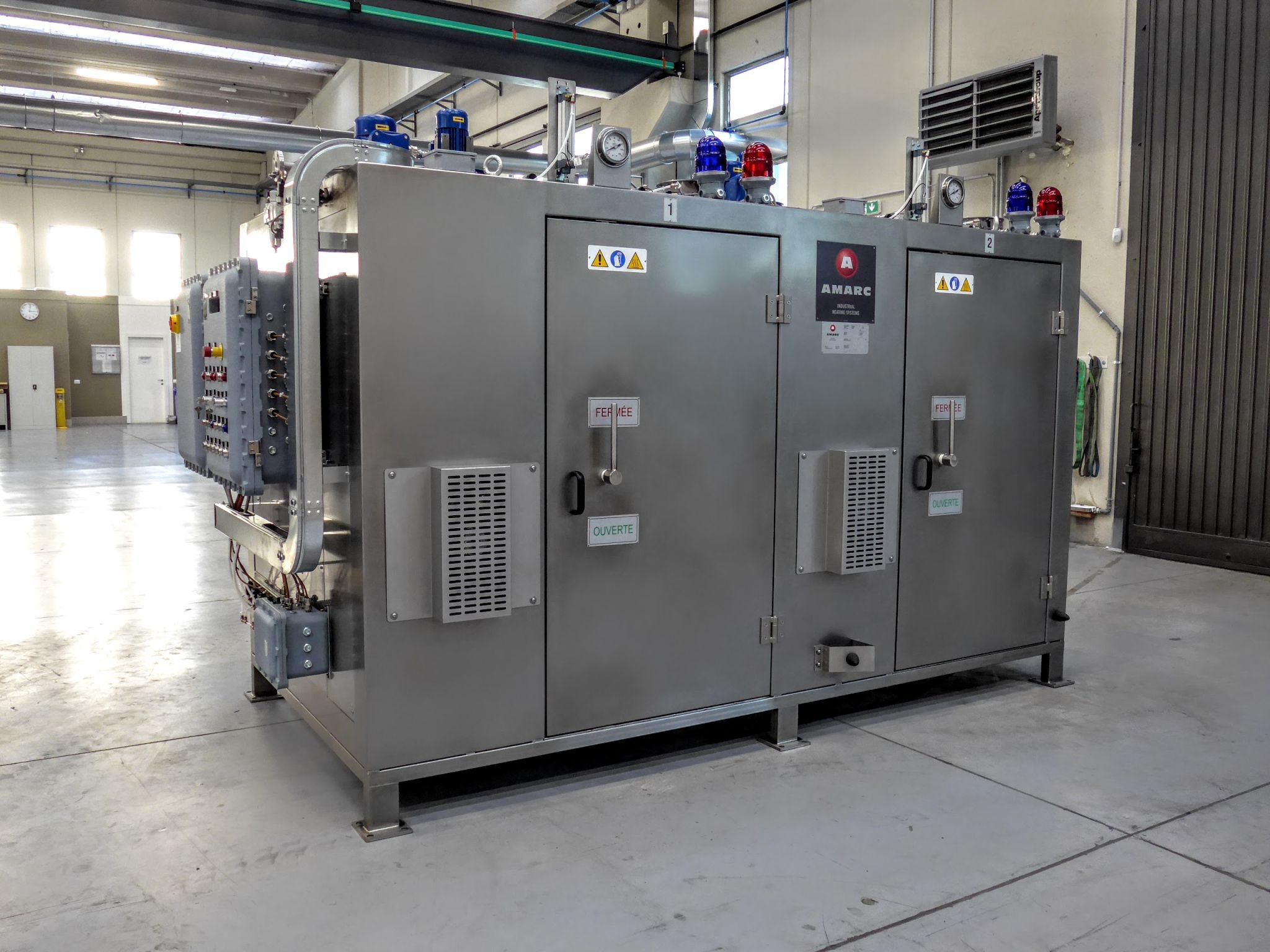
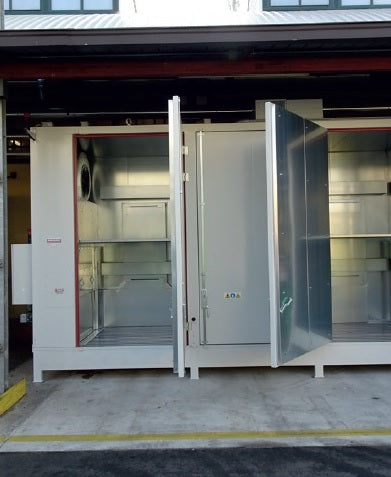
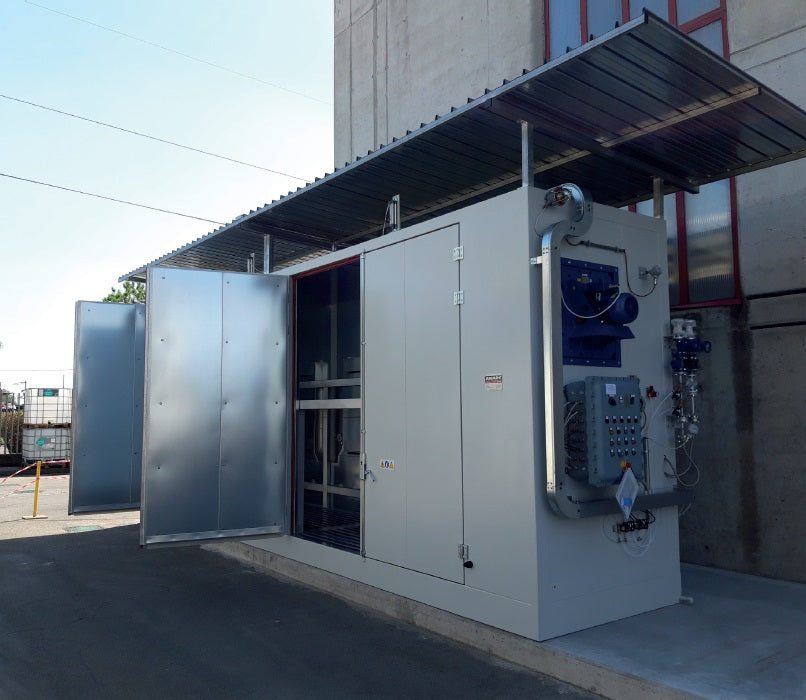